BLDC Motors Vs Other Types
There are many types of electric motors, ranging from tiny coreless DC motors used in cell phone vibrators and micro-drones to industrial 3-phase AC motors used in machines such as the one in Usibelli's Dragline.
The motor topology used in most multirotors however, is the brushless DC (BLDC)motor. These operate similarly to brushed motors, which were explained in the last video, however the commutation is done electronically. Eliminating mechanical commutation removes many of the disadvantages of a brushed DC motor, such as “the arcing generated between the brushes and commutator segments, the decay of the carbon brushes, the dust and pollutant reaching the commutator, and the shorts that could develop between the commutator segments. In addition, the mechanical commutation is noisy and generates electrical radio interference.”(El-Sharkawi, 127)
One disadvantage of the BLDC motor is the necessity of a motor driver, unlike the brushed DC motors, and most AC motors which can generally be directly connected to DC or AC sources respectively. Some small BLDC motors have built in controllers, like computer cooling fans, and other highly integrated motors. However, drone motors must be connected to a standalone electronic speed controller (ESC) to provide the right switching signal for a certain rotational speed.
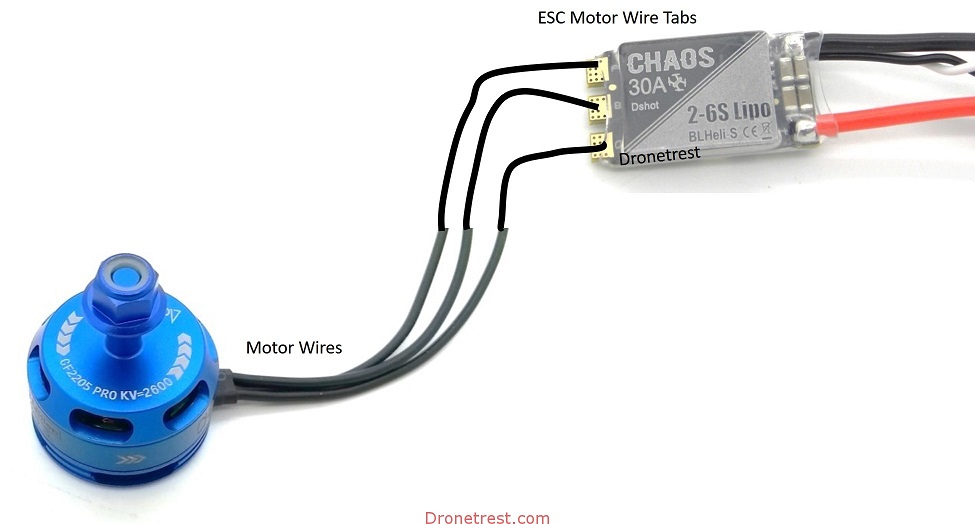