The Physics of
Fireground Hydraulics
Back
Next
Pump Construction
Pumps mounted on fire engines are relatively simple contraptions.
Most are midship mounted and are designed to put out 1500 to 2000
gpm. More often than not, a fire pump sits separate from the
drive shaft of the engine and can be engaged and disengaged.
Shifting into "Pump Gear" is just as simple as shifting to drive or
reverse. That being said, all fire pumps receive energy in roughly the
same pattern of energy transfer. The chemical energy in fuel
(diesel or gasoline) is released through combustion inside an
engine. The power stroke of said engine converts that chemical
energy to mechanical energy, which is transferred through the pistons
to the drive shaft. As the pump in engaged, a gear is lowered
from the transfer case onto the drive shaft. This system of gears
now energized in the pump turn an impeller.
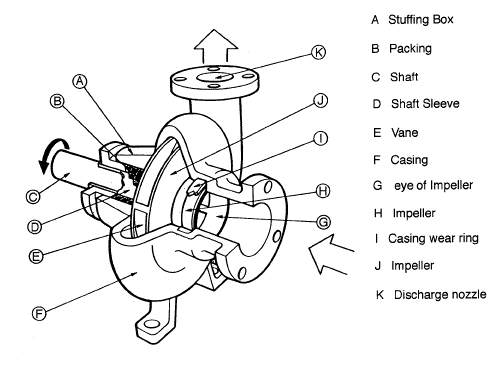
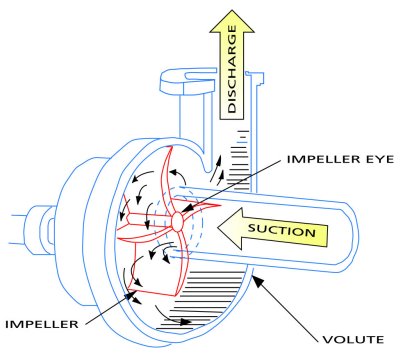
Shown here are two single stage impellers. As the impeller spins
at speeds in excess of 750 revolutions per minute water is drawn in and
spun out into the volute due to centrifugal force. The volute is
basically a section of piping that reduces in diameter. Since
Pressure=Force/Area, the decreasing cross sectional area of the volute
amplifies the compressional forces on the water, creating pressures
close to 300psi. Two stage pumps are also sold commercially, but
they are used more for high rise fire fighting operations due to their
ability to pump more gpm's at lower pressures. Otherwise, they
are more complicated and the difference in pressure to volume output
compared to single stage pumps is not as significant.