How Does It
Work?
The Motor
The ESP's motor is a very specialized piece of
equipment that has taken years of development. The
motor which is very small in diameter, is able to
produce an enormous amount of power, which is
translated to the fluid.
How Does it work?
The pump is connected by a very large electric
cable to a surface unit. From this surface unit, the
operator can control the power input, which controls
the fluid flow rate. The motor turns roughly at
3,500 rpm which is about 60-Hz power. Most units can
operate between 230 and 5000 volts depending on
fluid needed.
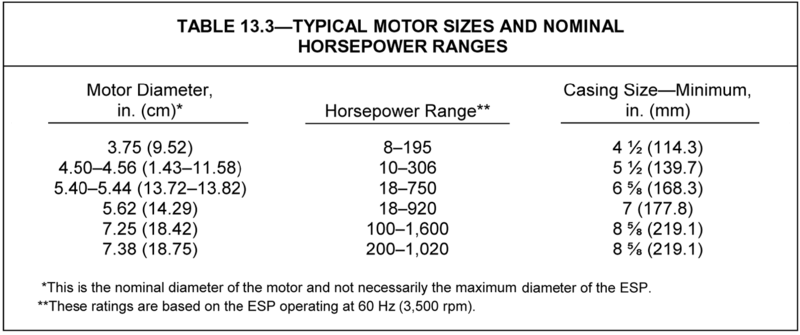
How is it constructed?
"A wound stator comprises an unwound stator,
electrical windings, and insulation and
encapsulation systems. The unwound stator has
thousands of electrical-grade steel laminations
stacked in the housing and is compressed to hold
them aligned and stationary. The laminations are
die-punched with a center bore for the rotating
components to fit into and 18 winding slots for the
winding wire. Each slot is insulated with a
very-high-dielectric-strength polyamide insulation
material. This slot insulation provides
winding-to-stator (turn-to-ground) electrical
protection.
Insulated copper wire called "magnet" wire or "mag"
wire is then wound into each slot to form three
separate phase coils displaced at 120° intervals.
The insulation on the mag wire provides wire-to-wire
(turn-to-turn) electrical protection. Also, at the
end of the lamination stack, where the coil has to
make a 180° winding turn ("end turn"), insulation is
placed between the first winding phase and the motor
housing and then between each phase. This protects
for phase-to-phase faults.
After the mag-wire winding and insulation is
complete, the wound stator is then encapsulated with
either a solid-fill epoxy or varnish coating. The
encapsulation process fills the voids left in the
slots and around the end-turn coils. This provides
several important functions. First, it mechanically
holds the windings to resist movement that causes
wire-to-wire rubbing and possible damage to the
wire’s insulation. Second, it adds dielectric
strength to the slot winding and end turns. Third,
it significantly improves the overall thermal
conductivity for better heat dissipation from the
motor core through the slots to the motor housing
skin. And last, it protects the winding from an
attack by contaminates such as wellbore fluid. The
last two are less significant for the varnish
coating method. As its name implies, it is just a
thin coating, mainly on the surfaces of the
lamination slots and the mag wire, and has voids
where motor lubricating oil accumulates, reducing
both the thermal conductivity and the dielectric
strength. (ESP Motors)"
A diagram of an ESP motor.
http://petrowiki.org/ESP_motors
Performance of Motors
The performance of the motor is essential to the
operation of the pump. Below is a typical performance
curve, the calculation for horsepower, and the
calculation for efficiency.
Horsepower
Efficiency
C
= constant = 3,960, where Q is in
gal/min, and TDH is in ft [= 6,750, where Q is in
m3/D, and TDH is in m]
N = rotating
speed, rev/min
T = torque,
ft-lbf
Q = flow rate,
B/D [m3/d]
ηp = pump
efficiency
Performance Graph
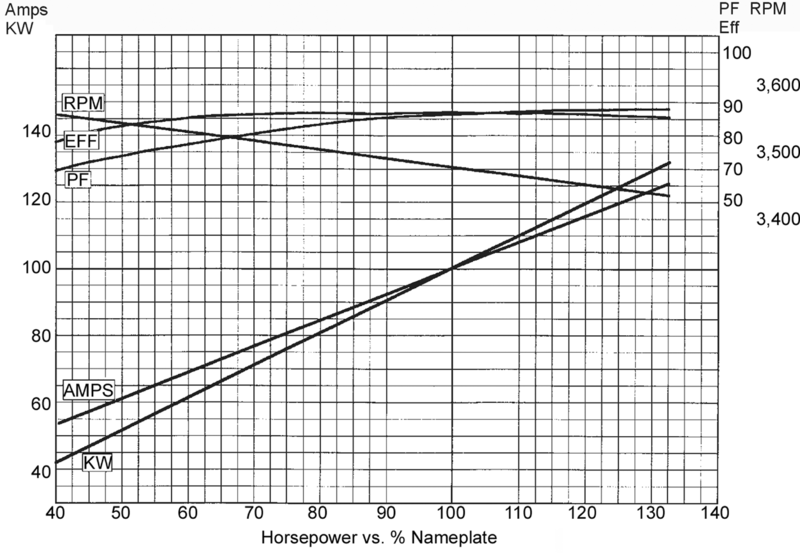
http://petrowiki.org/ESP_motors
Heat from the motor:
Since the motor is operating at extremely high
rpm's and almost non stop, it generates a lot of
heat. Due to the motor being mounted underneath
the pump, formation fluids are able to come into
contact with the outer casing of the motor. The
heat is then transferred into the fluid. This is
good in two ways. It not only cools the motor, but
it heats up the fluid which makes it more viscous
and easier to pump, as well as handle on the
surface.
To see an animation of an ESP,
click
here.