~VIOLIN~BODY~
The body of the violin is
created from wood, primarily spruce and
maple. Spruce is used for the soundboard
because it is light but longitudinally
strong as well as laterally flexible. It’s
most prominent feature is vertical graining.
Maple is a popular wood for the back of the
violin. The inner workings -- bass bar and
soundpost -- are created from spruce. The
fittings are made from dense hardwood:
ebony, rosewood, or boxwood. The modern
fingerboard is made from solid ebony whereas
the old violins used lighter hardwoods like
poplar and would cover them with maple,
ebony, or dyed wood veneer, since exotic
hardwoods were in short supply. There are a
number of reasons as to why one would choose
a specific wood over another, but when
creating a violin, wood is not simply cut
then glued together. According to
gussetviolins.com, violin makers prefer wood
grown at higher altitudes on northern
slopes. Wood is cut during the cold months
and seasoned (stored) in controlled
conditions for several years.
Even
after all of this newfound technology,
scientists continue to research and
analyse violins made by Stradivari and
Guarneri because there still seems to be a
mystery on how these instruments have
better sound quality than new violins
made. In 2008, an article was published
discussing how a CT scanner was able to
build a picture of a violin’s density
vibrations. The research found that the
overall density of the two groups (five
antiques by Stradivari and Guarneri versus
seven modern-day instruments) was about
the same, but the plates of the older
instruments had much more uniform density,
versus the new instruments. The homogenous
density of old violins makes them stiffer
and gives them more sound-damping
characteristics, producing greater sound
quality.
All parts of the
violins body; front plate, back plate,
sides, as well as the air inside, serve to
transmit the vibration from the strings to
the air around the instrument. If you
watch a violinist play, you can notice how
the violin is held only on the fingerboard
while the shoulder rest (used typically
although some people opt out of it)
prevents the player’s shoulder to directly
touch the back of the instrument. The
belly and back plates are made to vibrate
up and down at different frequencies. The
violin is being held at opposite sides of
the violins body and the vibration created
can be described as Chladni patterns.
Studies on Chladni patterns on the violin
have given violin makers and scientists a
better understanding of how the plates
should be processed in terms of scraping
when creating the final body shape.
|
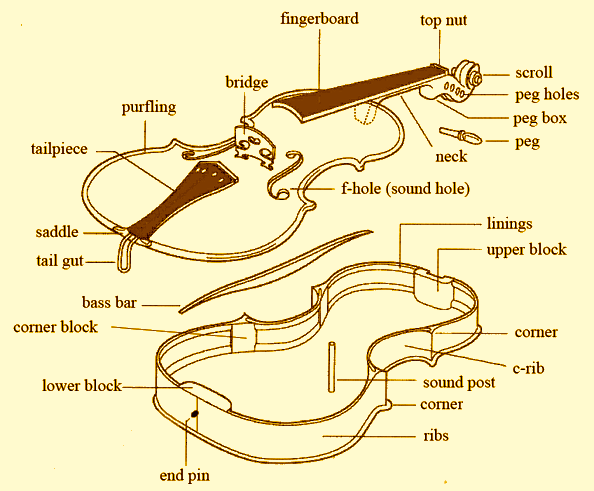
Source
Scroll - This is
located at the top of the violin. It is a
decorative part, mostly hand carved.
Pegbox - This is where the pegs
are inserted. The pegs are adjusted to
tune the violin.
Nut - Helps keep the distance of
the strings and supports the strings so
that it has a good height from the
fingerboard.
Strings - It has 4 strings that
are tuned a fifth apart.
Bridge - The position of the
bridge is essential as it directly relates
to the quality of sound produced by the
violin. The bridge is held in place by the
strings' tension. When the string
vibrates, the bridge also vibrates.
Fingerboard - It is a strip of
wood on the neck of the violin where the
strings are. When a violinist plays, he
presses down the strings on the
fingerboard, thus changing the pitch.
Sounding Post - Located under the
bridge, it supports the pressure inside
the violin. The bridge and sounding post
are directly related, when the violin
vibrates, the bridge, body and sounding
post vibrates as well.
F Holes - Is located in the
middle of the violin. It is called F Hole
because it is shaped like an F in Italics.
It allows sound to come out of the violin.
Altering the F Hole, such as its length,
can affect the sound of the violin.
Tailpiece - Holds the strings so
that it has a good distance from the
bridge.
Chin Rest - It helps the
violinist hold the instrument in place.
While playing, the violinist can use his
chin to hold the violin, thus freeing up
his hands.
|